
October 26th, 2024
The Importance of Soak Testing in Drilling Operations
Soak Testing: Ensuring Safety and Efficiency in Modern Drilling Operations
In drilling operations, soak testing serves as a vital procedure to validate the functionality and reliability of Blowout Preventers (BOPs) before deployment. By simulating various drilling scenarios and evaluating hydraulic circuits under maximum pressure, this testing method ensures that all components perform as intended. Strict criteria govern soak testing, requiring no visible leaks and minimal pressure drops during the evaluation. As an integral part of safety protocols, effective soak testing mitigates the risk of failures that could jeopardize crew safety and lead to costly operational disruptions.
In this blog, we'll explore the vital role of soak testing in drilling operations, highlighting how it verifies Blowout Preventers (BOPs) under simulated conditions. We'll discuss the testing process, its strict criteria, and advancements like Aquila's EDGE Kiosk that enhance effectiveness, all while emphasizing the importance of safety and reliability in drilling.
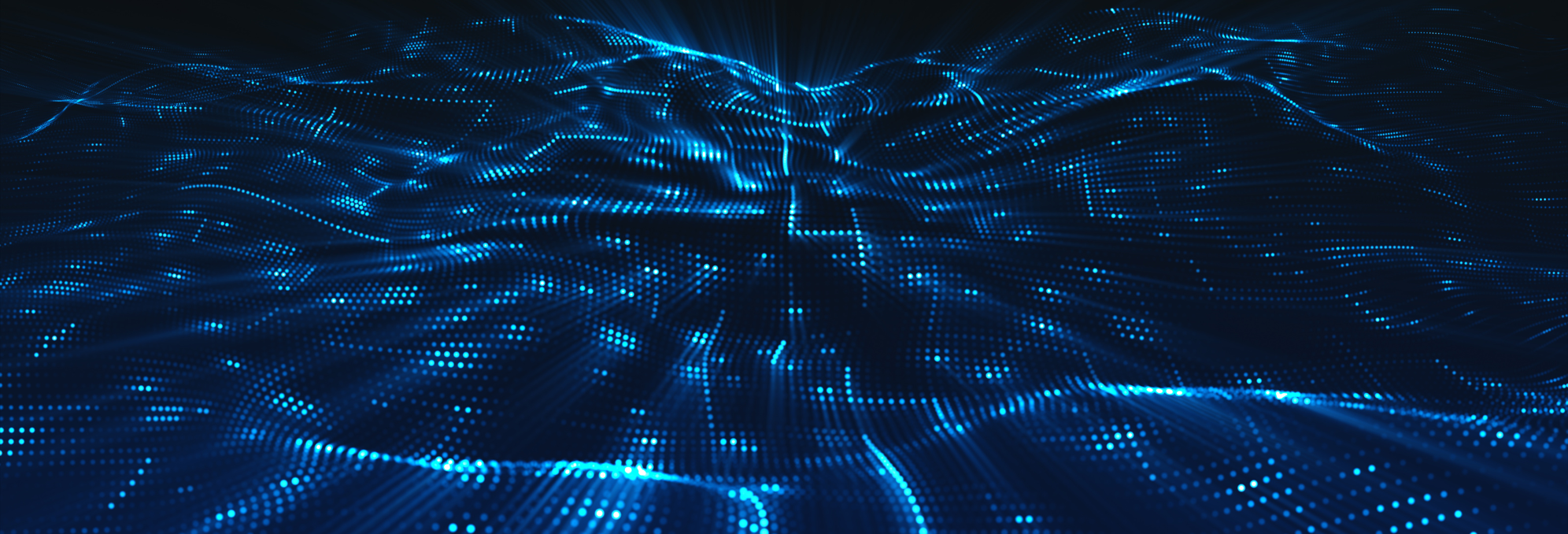
What Is Soak Testing?
Soak testing is a series of line ups that simulates the BOP in drilling and opposite drilling modes while testing the regulators at maximum pressure. Since you have shear rams and pipe rams this is typically divided into several different testing line ups to capture all possible scenarios including using drill pipe and without drill pipe. Most contractors have an internal procedure, which the subsea engineers must follow and document prior to ever deploying a BOP. Soak testing has very strict requirements for passing and is measured by an allowable drop in pressure over a specified time. For example, one test may be, all the shear rams must be in the “close” position with the regulators set at the maximum value allowed, and there can be only a 40 psi drop in pressure seen from those circuits over a 30-minute time period.
Soak Testing vs. Pressure Testing vs. Function Testing
Prior to deployment the Subsea department will perform pressure testing which is called stump testing. This is not the same and serves a different purpose than soak testing. Pressure testing is confirmation of the sealing rams and annulars proving that if the well being drilled, decides to send gas/oil or water pressure back towards the surface, the rams and annulars can withstand that pressure and will protect the crew and the rig.
Function testing is as simple as it sounds. The subsea engineers verify that when they press the upper annular “close” function from any panel or pod, that the hoses and tubing are hooked up correctly, and the upper annular closes as intended. This confirmation prior to deployment is exhaustive and covers confirmation of communication from the primary and secondary panels with verification no lines were accidentally crossed during the in between well maintenance period.
Soak testing is the verification of the hydraulic circuits that function the annulars, rams, connectors and valves, open/ close and lock/unlock. When the subsea engineer presses the button on surface, the BOP fluid travels from the surface pumps and accumulators to the subsea BOP, through a series of hoses, valves and many connection points, which are all vulnerable to failure. There is redundancy on all the systems to ensure everyone’s safety in case something fails, however, the BOP must be at 100% “verified” operational capacity prior to deployment subsea.

Why is Soak Testing Important?
Soak testing’s importance is twofold. The goal of any drilling operation is to drill a well safely and efficiently. Soak testing is integral to both goals. Before the BOP is allowed to be deployed the soak testing must meet two criteria to pass. One, there must not be any visible leaks noted during the testing period. Secondly, the pressure loss within any given line up must meet the aforementioned, pressure loss criteria. With the consequences of failure potentially being so high with the crew’s life on the line and the cost of failure, to pull the BOP to surface, verification of these testing criteria is crucial.
The Past:
The tools to measure soak testing in the past have been very basic. Subsea use pressure readbacks from hydraulic circuits during the soak testing line ups and manually track these pressures for hours to verify the system is “tight”. This means that we have no leaks from the pumps to the functions that are being tested. The visual criteria of seeing no leaks trumps any pressure readback and if a leak is noted, the test failed the criteria. The leak is then repaired, and the testing on that circuit will start over. Once the line ups and criteria are all met, the BOP would be deemed fit for service.
The Future - Aquila’s Edge Kiosk!
Aquila has now given the subsea engineers an innovative tool that goes beyond a basic level and utilizes new technology to give real time insight and verification prior to deploying a BOP. The EDGE Kiosk has been developed and implemented on rigs where the subsea engineer can line up the BOP for a soak test and the Kiosk will confirm the correct line up and measure more than just a readback pressure. The Kiosk can analyze what is going on with the BOP while the test is ongoing and gives the engineer not only the pressure analysis but also how the regulators have behaved during the testing. If the testing is completed successfully, a professional report is generated and can be used as verification of the BOP’s circuit and regulator reliability. If the test is unsuccessful the information provided to the Subsea engineer can be invaluable to help troubleshoot an issue that may be internal using data and trends. This assists in giving direction as to what needs to be investigated. The report generated so many advantages, not available before, such as troubleshooting analysis, cost justification, regulator behavior, and trending. The EDGE kiosk helps identify a problem or potential problem before we put the largest piece of safety equipment on a drilling rig, thousands of feet subsea.
With the costs being so high for failure, Aquila has given the oil industry a much-needed tool to bring reliability verification blended with innovation and technology. Regulations are only going to get more robust, and the customers’ expectations will only get higher as the industry continues to grow. Aquila’s EDGE kiosk is the future of soak testing technology.