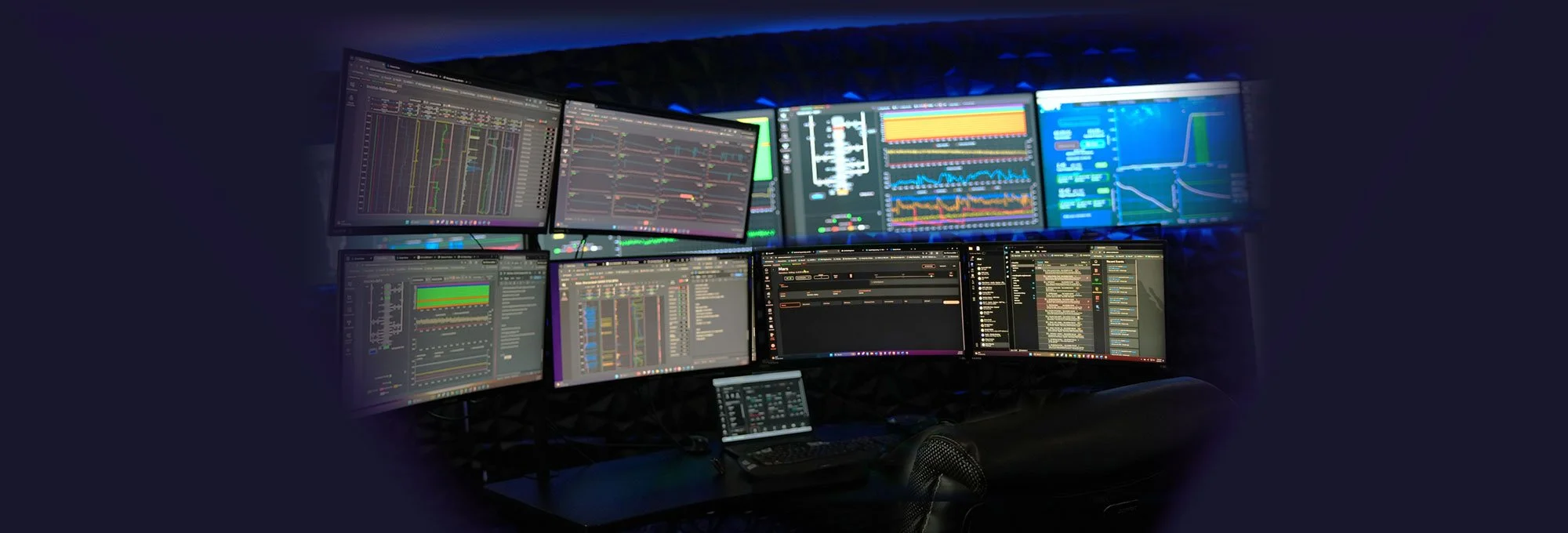
May 4th, 2024
Digital BOP Assurance (DBA)
Predicting the future with advanced BOP maintenance technologies
Industrial maintenance is vastly important to critical heavy machinery operations, the ability to predict equipment failure before it occurs represents a quantum leap in operational efficiency and safety. At the forefront of this revolution is condition-based maintenance (CBM), powered by cutting-edge technologies that do more than just monitor the current condition of equipment—they predict future failures.
This blog explores how our (DBA) Digital BOP Assurance technology is transforming maintenance practices by predicting when failures will happen, ensuring maximum uptime and reducing costly downtime.
Join our Newsletter to stay up to date on new Advancements, Announcements & more
The shift to proactive maintenance
Traditionally, maintenance has been either reactive or scheduled at regular intervals, without regard to the actual condition of the equipment. This often leads to either premature maintenance, which is inefficient, or to unexpected failures that cause operational disruptions and expensive emergency repairs.
The adoption of CBM, facilitated by our DBA technology, marks a significant shift from these traditional methods to a more efficient approach. By continuously monitoring the actual condition of BOPs and using data analytics to predict when maintenance should be performed, we can prevent failures before they occur.
How DBA works:
The technology behind prediction
Our DBA technology integrates a variety of advanced sensors and diagnostic tools that continuously collect data on BOP performance. This includes critical operational parameters analysis, Sophisticated algorithms and machine learning capabilities that will analyze the data to identify patterns or anomalies that may signal a potential failure.
One of the core strengths of DBA is its ability to learn from historical data. Over time, it becomes increasingly accurate in predicting potential issues, thereby enhancing its effectiveness in preventing unplanned downtime.
Real-World applications and benefits
Reduced Maintenance Costs
By predicting when maintenance is actually needed, companies can avoid unnecessary checks and reduce the incidence of costly emergency repairs.
Increased Equipment Lifespan
Proactive maintenance significantly extends the life of equipment by addressing issues before they cause severe damage.
Enhanced Safety
Predicting and preventing equipment failures enhances safety by reducing the risk of accidents associated with equipment breakdowns.
Operational Efficiency
Minimized downtime means operations run more smoothly and efficiently, with fewer interruptions.
Case Study: Success in the field
A recent implementation of our DBA system at a major rig demonstrated its effectiveness. The system predicted a critical pump failure, allowing for repairs during scheduled downtime, which saved the facility an estimated $1.2 million in emergency shutdown costs.
Conclusion: The future of maintenance
As we continue to refine our DBA technology, the scope of its capabilities continues to grow. The future of industrial maintenance lies in smart systems that not only monitor but also predict and adapt to the needs of complex machinery. By embracing these technologies, industries can reach new levels of efficiency and safety, positioning themselves on top of operational management.
The transition from traditional maintenance practices to advanced predictive maintenance isn’t just an upgrade; it’s a strategic transformation essential for any forward-thinking operation. Embrace the future with us and ensure your operations are not just running but advancing with time.
For more information on how our DBA technology can enhance your operations, click on the button below.